Search
Random EOF shutdowns from Klipper.
Hi everyone, a week ago my printer (heavily modified Neptune 3) started randomly shutting down in the middle of prints. I come back to a print with the "Klipper reports: SHUTDOWN / Lost communication with MCU 'mcu'" error message.
The printer has been "under construction" for the last couple of weeks, but it has been in varying states of "working" for most of the time - working well enough for me to print the parts I needed to get it back to "fully operational". During this time, the printer never shut down like it is now.
Only once I started making little cosmetic changes did the problem present itself. I was running a known-good print, and I got the above error twice (first time after ~2 hours, second time after ~1 hour) before I got a successful print off of it. This was last week.
After this successful print, I continued other prints with no issues. After a day or two with no problems, an hour long print threw the error at me four consecutive times between 10-45 minutes into the print. This is when I started looking into my klippy log and found some relevant articles citing things like EMF interference, bad power supplies, faulty cables etc. I realized that one of the changes I had made rerouted the printer USB cable right around the Z-stepper, so I rerouted it to how it was originally and immediately managed a successful print. This was 5 days ago.
After moving that cable I had no issues with printing several-hour long prints... until last night. I had been printing all day, then the problem came back. After one print finished, I queued up another print with a plate full of parts, it failed after 1.5 hours. Tried the same print again, failed in 30 minutes. I re-sliced to only a handful of parts to see if I could get those to print before the error occurs, and it's failing 15 minutes into the print.
The printer power supply is the unit that came with the Neptune, and it isn't powering anything besides stock hardware (exception being the SKR mini board), so I don't think it's that. The pi is on a quality unit. The USB cable has been working for a long time so I also don't suspect that, but I'm probably going to buy a new one today just to be sure. I adjusted my enclosure setup so that the Pi and SKR are able to get cool air (at one point had a personal fan pointing at the open electronics box, still failed).
Here is a link to my most recent klippy log (abridged to the start of the last failed print). I'm not very familiar with reading through this and finding oddities, but I do think it's strange that it seemed to load my preheat script in the middle of printing right before the EOF error. (It should be noted that this preheat script was made 1 or 2 failed prints before this most recent one, so it isn't the source of the error as prints were failing before the script was made). If there's anything I'm missing or something else I can try, please let me know!
Edit: While typing this post, I was running the same failed print without filament and both heaters turned off. It ran for about 45 minutes (most recent failure occurred at 12 minutes) so I cancelled the print and started it again with heaters turned on, still without filament. It again ran for about 45 minutes, so I again cancelled it and started the print again, this time with filament loaded. It failed in 5 minutes.
Edit 2: A test print with heaters on and no filament failed after 1h8m. So it isn't an issue with extruding filament.
Edit 3: New cable with the 5v leads taped off per @[email protected]'s advice. Ran the print without filament until completion. Reloaded the same file with filament, print ran without issue until the 1h14m mark, at which point I tapped my Klipperscreen device to wake up the screen, and as soon as it displayed the status, the printer errored out. This can't be a coincidence, can it? Whenever the print goes unmonitored for a long time, it fails as soon as I do something (load mainsail, turn on the klipperscreen) to check the status of it.
Big stringing problem with flsun SR and Orcaslicer
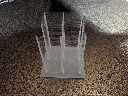
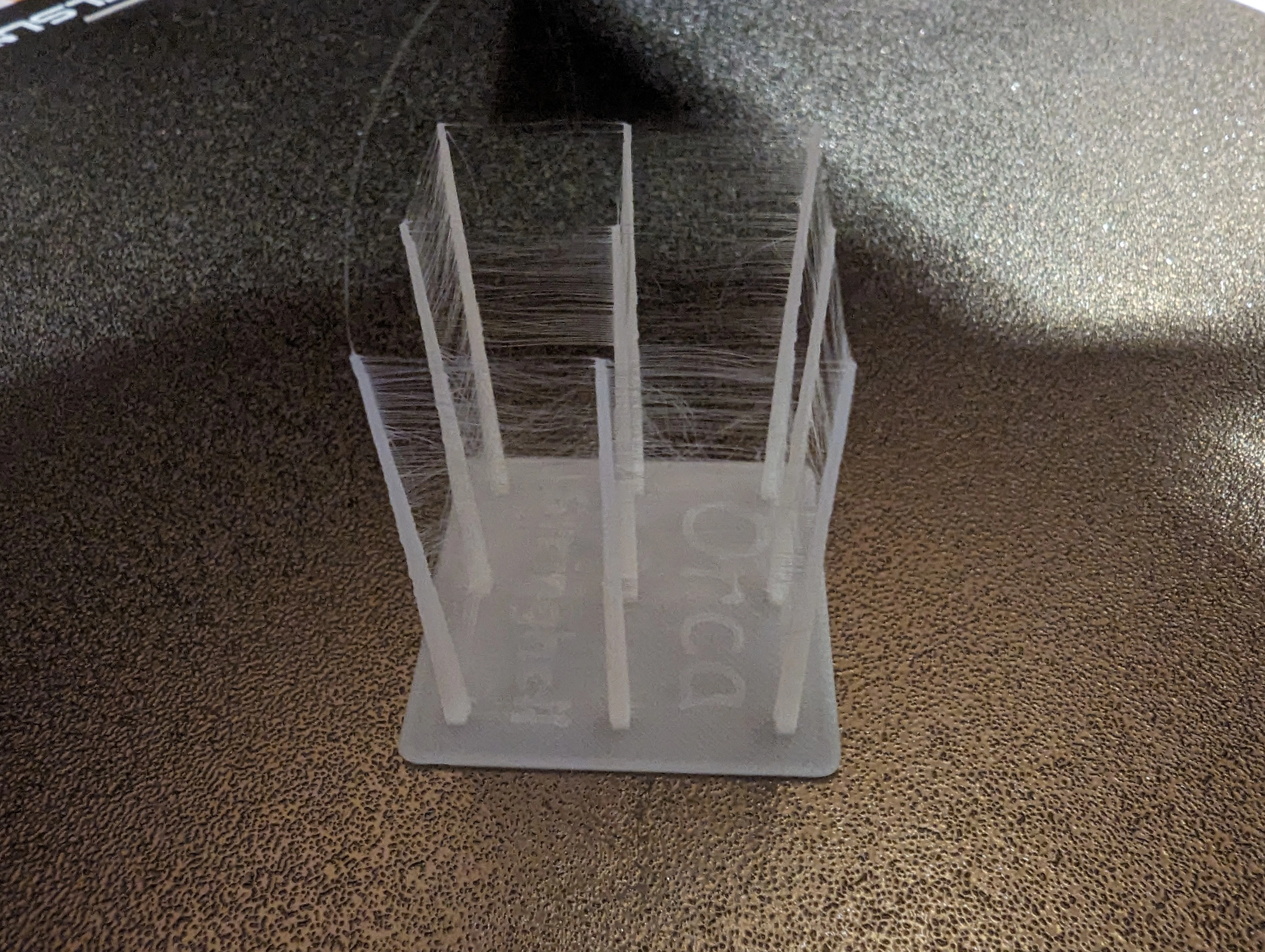
Ok guys, I'm breaking down and posting here to see if anyone has any ideas. I'm greatful for any advice.
I have an upgraded flsun SR. I recently lost my computer (psu issue, waiting for replacement) and I took this opportunity to switch from Cura to Orcaslicer.
Over-all I'm very happy, and getting some good speeds, but I just cannot remove stringing no matter what I try:
- Retraction from 0-7mm. After about 3mm, no further effect
- Retraction speed from 30mm/s-50mm/s. No noticable effect
- Travel speed and acceleration both high (up to 350mm/s and 6000 accel. No effect
- Temp from 205-215 with no effect
- Dried filament and different colours, no effect
- Wipe on retract on and off, up to 2mm wipe distance and 100% retraction. No effect
- Messed with scarf seams on and off, no effect
- No effect from layer heights
My setup:
- Printer - FLSun SR running klipper with a speede pad
- Filament - Esun PLA+
- Upgrades - Deported fans, OMG v2 extruder, volcano hotend and high flow cht nozzle
Clog Guy is back, and things have completely ceased making sense.
Hi guys. Please check my previous post for any background questions, I don't have it in me to go over everything again.
Long story short, I was having issues with clogging that were being caused by my hotend not reaching the reported temp. After a few days of troubleshooting and diagnosing the motherboard and Klipper settings, I gave up and decided the motherboard was faulty (even though I could not perform any tests to determine in) and bought an SKR mini. I got that all set up, and the printer has been working flawlessly since then.
Until now.
Same exact problem; one print goes perfectly fine, next print, failing to extrude by the 4th layer. I removed the clog, restarted the print, now can't even extrude the priming line. Fearing the worst, I disassemble the hotend, try hand feeding filament, and once again I am unable to push more than a few centimeters through before it gets clogged up. A probe thermometer reads ~160C while Klipper reports 200C.
What could possibly be happening here? The board is an aftermarket replacement from a completely different company, so I doubt it's a recurring manufacturer defect, but I have no idea what else can be causing this.
At this point I've spent so much time and money trying to fix this printer that I could almost buy a new one, but at this point I'm not convinced even that would solve the problem.
It's the clog guy again - temp readings are bad!
OK guys, I finally found what the issue is, or at least kind of where it's coming from.
As some of you (and myself) suspected, my hot end is not reaching the reported temperature. I previously blamed the low readings on my IR thermometer on not being able to point the laser directly at the hotend, but it seems it was reporting accurate readings (around 95C when klipper reports 200C).
Now, here's where things get a little weird. At this point, I've used multiple thermistors, but swapped in a new one anyways. My board also has a pin for a second extruder thermistor, so I plugged it in to that one and changed the pin in my printer.cfg. No change.
I tried switching the bed and hot end thermistors on the board and in printer.cfg, no change.
I changed the thermistor "sensor type" from "EPCOS 100K B57560G104F" (same as the bed) to "Generic 3950", no change.
I found an article about tuning your pullup_resistance value. My cfg file did not have this value specified, so I added a line and started with the default of 4700, which made no difference (I'm assuming this value is loaded from the sensor type by default?). I toyed with the values until my thermometer read ~220C when setting the printer to that temp. However, to achieve this I had to adjust the pullup_resistance from 4700 to 13k+ (far beyond what should be needed) which makes klipper report 6C at room temp (print bed reports 27C). Unsurprisingly, I can hand-feed all the filament I want, but the temp reading is only now only accurate at 220C rather than only being accurate at room temp.
The thermistor, I feel, can be removed from the suspect list, as multiple thermistors exhibit identical properties.
I also feel the motherboard can be removed as well; there are three pins for thermistors, all three show accurate readings for the bed but identically inaccurate readings for the nozzle.
This only leaves software/ firmware, which I find incredibly odd for three reasons. For one, the printer was not even shut off in between "working" and "not working"; I successfully completed a print, and without shutting down, updating any configs, changing any settings etc., I swapped out the nozzle, and the printer hasn't worked since. Second, both the bed and nozzle thermistor are configured exactly the same, so if the nozzle is not set up properly the bed should be wrong too. Finally, Klipper is really straightforward and it's easy to configure things that commonly need configuring, it doesn't seem right that a configuration got changed and I'm completely incapable of finding what happened and fixing it.
As a Temporary FixTM, I'm inclined to get a nice reliable probe thermometer, calibrate a pullup resistance value for common print temps, then updating my cfg whenever I want to change temps more than ~5c. This is obviously not even close to an ideal solution, but I don't know what else to try. Everyone else I've seen with this issue has resolved it either through hardware replacement or fixing settings, and I've tried all I can with both.
Clog test write up - this time with pictures!
First I'd like to say thanks to everyone for looking at these posts and trying to help, and sorry to anyone who may be annoyed. Trust me, I'm not happy either.
I'm jumping back and forth between making this write up and recreating the clog by hand feeding filament into the hotend. This test was already performed earlier today and I got the same clog as I have been, so the extruder can be removed from the list of possible culprits. Anyways, here's the steps I'm following:
1. Verify temperatures are within acceptable range
This is my temp chart upon starting the printer. I used a thermal laser to test both nozzle and bed and they were within the range of accuracy of the laser. The laser is not accurate enough to get a good reading on the heat block; however, a few drops of water on the heat block boils within seconds when the temp is set to 100C, whereas at 90C it does nothing, so the nozzle is accurate at least to this temp.
2. Assemble hot end
This is what my hotend assembly looks like without the nozzle or bowden tube. It should be noted that my printer has been modified such that the bowden tube going from the extruder is fed all the way through the heat sink to the nozzle, rather than having a fixed tube inside the heat break. I understand that this modification itself could introduce the issue I'm facing, but the issue started before the mod was done, so I don't think it is the cause.
Nozzle cleaned with blow torch and wire brush.
Underside of the heat block. The picture makes the threads look a lot worse than they actually are, in the photo it looks like some sort of gunk or shavings are at the end but after inspecting the block and scrubbing it with a wire brush there isn't anything there. The nozzle also threads in without any issue.
With the heat block at 100C, I first loosely attach the nozzle, then insert the Bowden tube so its against the nozzle. Since I'm hand feeding filament, I'm only using ~10cm of tubing. For photographing purposes, I put a small notch on the tube at the top of the coupling (not visible in this photo). Then, with the coupling depressed, I finger tighten the nozzle, pushing the tube out slightly.
Here you can see that the nozzle is not getting tightened against the heat block (the small gap between the face of the nozzle and block); this verifies the nozzle is flush against the heat break.
I've circled the notch mentioned previously - this shows that the nozzle was indeed pushing the tube out of the coupling, and should verify that there is no space in between the bowden tube and the nozzle inside the heat break. With all this verified, I use a wrench to tighten the nozzle ~1/4 of a turn without depressing the tube coupling. This should ensure a tight mate between the tube and nozzle. I also put another mark on the tube at the coupling to make sure it does not move during the test, and reinstalled the fan shroud.
3. Hand feed filament
I'm quite frustrated because at the time of typing this I've repeated the above steps twice now, because when I went to hand feed the filament it instantly became clogged and I was not able to get any good data, but finally on the third attempt I've got a solid clog. I'm waiting for the hotend to cool off so I can remove it and get some pictures. Meanwhile, I'll explain that the hotend was heated to 200C and I hand fed some filament through it. As stated, the first two times it clogged instantly, but even when I was able to get filament to run on the third try it was incredibly difficult, when it has always been very easy to hand feed PLA at this temp. (When I did this test earlier, I tried increasing the temp to 240C, which made it a little easier to feed and prolonged the clogging slightly, but ultimately ended the same.) Eventually, it got to the point where I was almost breaking the filament trying to force it through, until I couldn't get any more to go at all. I'd guess this was maybe 20cm of filament.
Hotend is cooled off, I managed to removed the nozzle, clog, and bowden tube all in one piece so that is awesome. This is exactly what I've been experiencing over and over again:
A clog forming between the nozzle and bowden tube, filling the diameter of the heat break.
The Bowden tube has been pushed out of the coupling by about the thickness of the clog. It should be noted that the coupling was actually replaced a few weeks prior to the problem starting, but I've since tested both another new coupling as well as the one that was originally replaced, and all three behave the same. I can also support most of the printer's weight by pulling up on the Bowden tube. Thus, I believe the slipping coupling to be a symptom rather than the cause.
This is what my heat block looks like after I repeated the test with some gray PLA. (A different nozzle as well as a different coupling was used for this test.) I noticed when putting the nozzle back on that it was really difficult to do so, and it seems like this could be why: filament making its way into the threads during the clog. (I guess my previous statement of the block being cleaner than it looked was probably false...) During earlier testing, I've soaked and torched the heat block to make sure this buildup wasn't causing the clogging, but again it seems to be a symptom rather than the cause.
The two clogs on the left are from earlier tests using the printer's extruder, the two on the right are from tonight's hand fed tests; note the difference in thickness of the clogs, the extruder is much more capable of pushing through the clog than I am which results in the clog getting much larger before failure. It should be reinstated that this exact result is prevalent across multiple filaments and nozzles. I was not able to get such clear results of what was happening when I had the all metal heat break(s) installed, and unfortunately I don't have the time tonight to swap one in, but it was clogging with more or less the same behavior, so I'd have to assume it was clogging between the Bowden tube and heat break. Before the hotend was modified, all of the common steps were taken to verify the internal bowden tube was functioning properly, and the bowden tube installed now is probably the third one that I've cut off of a brand new Capricorn tube since this problem began. I'm considering re-modifying the hotend to work how it did stock, but again it was clogging when it was set up the original way so I don't think this is the issue. I'll probably try it out tomorrow if nothing else gets me anywhere,
I have to go to bed before I can continue any more testing, but I'll get back to any comments or advice as soon as I can tomorrow. Yesterday was the first day I managed to pull one of those perfect clogs out, now that they've been coming out consistently like that I feel I'm much closer to finding the problem than before. Please let me know if anything needs to be clarified or if I missed anything, my hope is this thread (and my suffering) might help someone with a similar issue.
Cannot fix a clogging issue.
Hi everyone, I'm having constant clogging issues with my printer that sprung up out of nowhere. I'm running out of things to test.
The printer had been running several prints a day for several days when I decided to change nozzles for one print. Ever since then (~2 weeks ago) i have not completed a single print, due to clogging. I have tried:
Replacing the PTFE tubing in my hotend.
Replacing the nozzle. (I've used a handful of nozzles, all with the same results)
Trying different filament.
Replacing the hot end with an all metal hot end, trying three different heat breaks from two manufacturers.
Removing the printer from its enclosure to ensure proper cooling.
Adjusting extrusion tensioner.
All the other basic obvious stuff like making sure there's no blockages anywhere (whole hot end and nozzles have been soaked in acetone, torched, brushed etc).
The printer will seem to work fine for a little while before either slowly failing to extrude until it completely jams, or it completely jams all at once. I don't think it's heat creep, because I tried setting the nozzle to printing temp, letting it sit for half an hour or so and running filament through it and it had no issue, whereas prints usually start to fail within the first 10 minutes. It also doesn't have anything to do with my print settings because I'm able to get it to clog sometimes by just running the extrude command.
I'm completely at a loss here. I don't know what else to try. Does anyone have anywhere else for me to look?
Update: I tried detaching the heat block from the rest of the printer and running filament through the (cold) heat break, and it got clogged. There was a small bit of filament adhered to the inside of the heat break. So it's apparent that's where the clog is forming, it's just a matter of finding out why it's happening. Everything seems to point towards heat creep, but even when I intentionally try to heighten the conditions that to cause heat creep I can't intentionally replicate the clog. I'll keep experimenting down that route, though.
Update 2: After clearing that clog, I noticed the short piece of Bowden tube between the top of the heat break and the top of the heat sink was slightly too short. I modified the heat sink to bypass this short piece altogether; the Bowden tube now goes directly from the extruder into the heat sink to the top of the heat break. I also applied a thin layer of thermal paste to the outside of the heat break to ensure good contact/ heat transfer with the heat sink.
After doing all of this, I ran a PID tune and, with my AC set to lower than average, started extruding filament. After extruding ~300mm of filament, I tried a few nozzle and filament swaps using very careful techniques to avoid leaving any residue. I'm able to pull the filament out in a solid piece to where I can see light through the nozzle afterwards. Then, finally, out of the blue, the clicking returns. Another clog. I wasn't able to remove the filament as cleanly this time to inspect the clog, but I'm strongly suspecting heat creep at this point, despite going above and beyond to mitigate it. It's quite late though and I've got work tomorrow so it'll have to wait until then.
Fluidd randomly shows a blank screen on specific browsers, while others work fine.
Hi guys, I've dove into the klipper scene with my Neptune 3 and am having a really odd issue.
When I first got klipper/ Fluidd set up, I tried loading the interface in my browser (Chrome) and got an all white screen. At first I thought it just failed to connect, or the process wasn't running, but then noticed the tab was named "Fluidd". I spent an hour or two reinstalling things over and over before I decided to try a different browser (Edge). It loaded up just fine. I pulled it up in Firefox and spent a while configuring it. I had to reinstall the Pi's OS a few times, but each time Fluidd came up in Firefox without issue but failed to load in chrome.
Now, suddenly, it is failing to load in Firefox, but continues to load in Edge. Below is a screenshot from my PC with all three browsers with the same address typed into the bar, with only Edge loading for some reason... Does anyone have any clue what could be causing this? It also loads on the Chrome app on my phone.
Adhesion issue
I am somewhat new to 3d printing and i am playing around with different filaments and print plates on my cheap ender3 v3 se.
Right now I am observing a weird adhesion-issue i have not seen before: The copper-silk filament has trouble sticking to the printplate, but only in some places of the plate.
My guess it's either some dirt/oil on the printplate. Or maybe the silk-pla has bad adhesion.
What do you think?
This printplate is this (but glued over the original printplate): https://www.amazon.de/dp/B0CL5FYHBR
The filament is this: https://www.amazon.de/dp/B09CPBRQXS
some clarification for the video: all corners of the first layer should have been rectangular. Instead some corner lost adhesion and become roundish. Here is the view from the slicer: https://imgur.com/rwA0fQW